The Wet Etching Process
Typically a wet etching procedure can merely entail dissolving the substance to be removed in a liquid solvent without affecting its chemical composition.
On the other hand, a wet etching method often entails one or more chemical processes that use the original reactants while producing new species.
Three important processes can be broken down into a basic wet etching process:
Etchant diffusion to the surface for removal
The reaction of the liquid etchant with the substance to be etched. In most cases, a reduction-oxidation (redox) process occurs. The oxidation of the substance is followed by the dissolution of the oxidized material in this process.
Diffuse of the different reactions which resulted of the reacted surface.
Reduction-oxidation
Different reduction-oxidation (redox) reactions are typically common in wafer fab wet etching techniques, in which an oxide of the material to be etched is first generated, when dissolved, leading to the development of another oxide, which is then dissolved, and so on until the desired material is consumed.
Selectivity
The etchant’s ‘selectivity’ is another key element in every etching procedure. Not only does an etchant affect the material being removed, but it also attacks the mask and the substrate (a kind of surface beneath the substance being etched).
The capacity of an etchant to remove just the material desired for etching while leaving behind the mask and substrate materials intact is commonly referred to as ‘selectivity.’
The ratio between the etchants diverse etches rates for different materials is used to calculate selectivity, S. As a result, a suitable etchant must have a high selectivity value for both the mask (Sfm) and the substrate (Sfs), specifically.
The etching rate for the etched film must be substantially greater than the etching rates for the mask and the substrate.
Wet etching of silicon
A combination of nitric acid (HNO3) and hydrofluoric acid can be used to wet-etch silicon (single-crystal or poly-crystalline) (HF). The nitric acid typically consumes the silicon surface to form a silicon dioxide coating that the HF then dissolves. The general response is as follows: Si + HNO3 + 6 HF –> H2SiF6 + HNO2 + H2 + H2O. As previously specified, silicon dioxide may be wet-etched with a number of HF solutions.
Benefits of wet etching
Regardless of its resolution limits, wet etching is still widely used due to the following benefits:
- It has a low price
- The process has a high level of reliability
- High efficiency
- In most circumstances, excellent selectivity concerning both mask and substrate materials.
- Increased usability
- Greater repeatability
- Increased efficiency in the application of etchants.
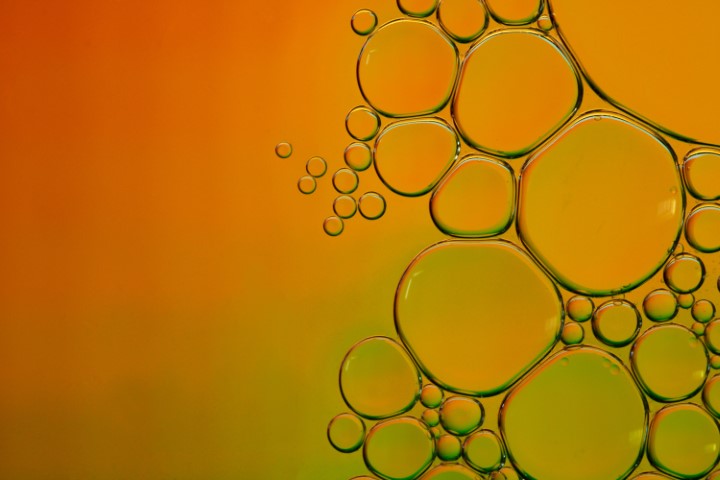